Fiber optic strain sensor pdf
Fiber Optic Distributed Strain and Temperature Sensors (DSTS) BOTDA Module For more information about our strain and temperature sensor system and related products, please visit www.ozoptics.com Photo: 2U+1U PC computer chassis shown.
Opsens Solutions’ fabrication processes ensure an exact definition of the gauge factor, making OSP-A sensor the most accurate fiber-optic strain gauge sensor in the industry.
optic sensors are non-intrusive and easy to install—thousands of sensors can be installed in less time than conventional strain sensors—and the system is capable of processing information at the unprecedented rate of 100 samples per second.
J. R. Moore et al.: Rockslide deformation monitoring with fiber optic strain sensors 4.2 Fig. 5. (a) Expanded view of the transient step occurring on 28 April 2009.
3 Related Products OZ-GuardTM Fault Finder The OZ-GuardTM Fault Finderis an OTDR-based product that detects and locates breaks or major bends in fiber optic cables.
Polarization mode dispersion effects in embedded fiber optic strain sensors A. Eyal, M. Ben-Artzi, 0. Shapiro andM Tur Faculty ofEngineering, Tel-Aviv University, Tel-Aviv, ISRAEL 69978
1 Application of a Fiber Optic Distributed Strain Sensor System to Woven E-Glass Composite R.F. Anastasi U.S. Army Vehicle Technology Directorate, ARL, AMSRL-VT-S, Nondestructive
The HBM FiberSensing range of optical (FBG) strain gauges and sensors is the perfect choice for demanding testing and monitoring applications. Previous Next High-Performance Optical Fiber Sensors
In push–pull fatigue tests of an aluminum alloy, the plastic strain amplitudes measured by three optical fiber sensors differed by only 0.43% at cyclic strain amplitudes of ±7000 με and 1.9% at cyclic strain amplitudes of ±8000 με. We also applied the sensor on an extruded magnesium alloy for evaluating the peculiar asymmetric hysteresis loops. The results obtained were in good
Fiber-optic Bragg grating strain sensors hold a great deal of potential for structural monitoring because of their exceptional stability and demon strated potential for long-term monitoring. This
The strain sensitivity of the Bragg wavelength arises from the change in the pitch of the fiber grating due to strain and changes in the refractive index arising from the strain-optic effect. When a strain is applied to the grating, the Bragg reflected wavelength changes. The wavelength shift Δλ
fiber may break already at low strain levels. To measure strain the sensors must be fixed to the specimen, typically by gluing. Stretching a strain gage sensor causes a change in resistance of …
optical fiber link, and numerous types of athermal fiberoptic sensors. The central system is The central system is comprised of a tunable light source, a receiver, and a microprocessor unit.
FIBER OPTIC SENSORS FOR STRAIN MONITORING IN ICCM

Pico-strain multiplexed fiber optic sensor array operating
PDF An extrinsic Fabry-Perot interferometric (EFPI) fiber optic sensor is presented for measurement of strain at high ambient temperatures. The sensor is fabricated using a femto-second (fs) laser.
Fiber optic strain sensor for oil&gas, energy, structural health monitoring, defense & aerospace, geotechnical, civil engineering, microwave chemistry, food, environments with high electromagnetic interference, industrial applications and research
National Aeronautics and Space Administration Real-Time Fiber Optic Strain and Shape Sensing (FOSS) Technology In-Space Non-Destructive Inspection Technology Workshop
Distributed fi bre-optic temperature and strain measurement with extremely high spatial resolution 1 Fibre-optic sensor technology For many years, fi bre sensors have meas-ured temperature or mechanical quanti-ties, particularly in environments where electrical sensors reach their performance limits; this may occur in environments with large electromagnetic fi elds or diffi cult chemical
Fiber-optic sensors (also called optical fiber sensors) are fiber-based devices for sensing some quantity, typically temperature or mechanical strain, but sometimes also displacements, vibrations, pressure, acceleration, rotations (measured with optical gyroscopes based on the Sagnac effect), or concentrations of chemical species.

Fiber Optic Strain Sensors. Fiber Optic Strain Sensors are used for accurate deformation measurement along the entire length of the fiber without the need for temperature compensation. View products; Linear Position Sensors Linear Position Sensors. Linear Position Sensors convert displacement of an object into an output signal. View products Show subnavigation ← Back to …
www.lunainc.com 1 Riverside Circle, Suite 400 Roanoke, VA 24016 solutions@lunainc.com 1.866.586.2682 Application Note EN-FY1701 Revision B May 30, 2017
E10190-000816 FOS Page 1 1 PRODUCT 1.1 INTRODUCTION The SENSOPTIC line of fiber optic sensors are specially developed instruments that can
hydrophone sensors is a measurement of fiber strain via the strain induced phase change in a light field. A large-scale sensor array system requires many channels multiplexed onto a single fiber,
The optical fiber is connected to a light source and when the light encounters the strain FBG sensor, a specific wavelength is reflected based on the properties of the gratings. As the FBG expands or contracts, so does the gap between these gratings, therefore changing the reflected wavelength of light. The reflected light is then measured and the shift in wavelength can be converted to a
This communication reports on a novel intensity-based optical fiber strain sensor. A conventional multimode fiber was drawn-down to give a reduced cross section that resembled a symmetrical taper.
Smart Mater. Struct. 17 (2008) 035033 T Mawatari and D Nelson Figure 2.2. Coordinate system of a multi-parameter sensor. equations, p 11 and p 12 are the strain–optic coefficients, also
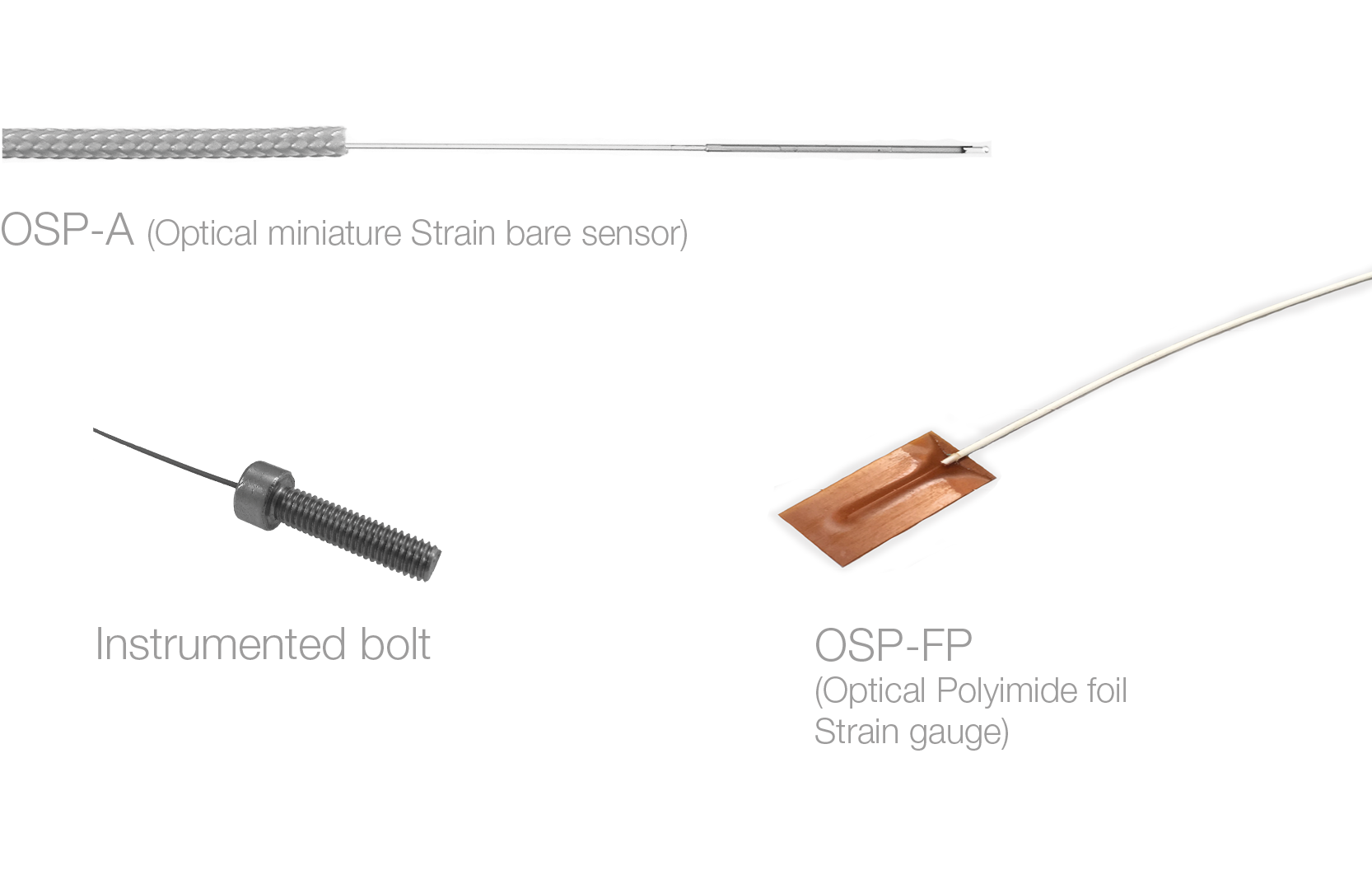
Hide aki MURAYAMA et al.: Structural Health Monitoring by Using Fiber-Optic Distributed Strain Sensors With High Spatial Resolution 357 yachts were equipped with fiber-optic distributed
Optical-fiber sensors have become key tools for strain measurements, with sensitivity limits ranging between 10−9 and 10−6ε hertz (Hz)–1/2 (where ε is the fractional length change). We report on strain measurements at the 10−13ε-Hz–1/2 level using a fiber Bragg-grating resonator with a diode-laser source that is stabilized against a quartz-disciplined optical frequency comb, thus
Nonlinear fiber-optic strain sensor based on four-wave mixing in microstructured optical fiber Bobo Gu,1,2,* Wu Yuan,1 Michael H. Frosz,3 A. Ping Zhang,2 Sailing He,2 and Ole Bang1
PDF For many applictions it would be highly desirable to be able to measure all three axes of strain and temperature internal to composite materials. Conventional electrical strain gauges are
Smart Mater. Struct. 17 (2008) 035037 KTWanet al Figure 1. Illustration of the strain sensor with shear lag under uniform strain field. Adhesive Optical Fiber on top of the component
Fiber Optic Distributed Strain and Temperature Sensors
Fujikura Technical Review, 2010 13 Fiber-Optic Strain Sensor with a Millimeter Class High Spatial Resolution Hirotaka Igawa,1 2Hideaki Murayama, 4Yuichi Machijima,3 Koji Omichi, Yoshihiro Terada,4
All fiber optic sensing methods rely on either (1) the longitudinal deformation of a sensor fiber caused either directly by axial strain, or indirectly via the Poisson effect through lateral pressure on the fiber, or (2) the photoelastic effect which results in refractive index changes in the core and cladding materials of the fiber.
Preface This report describes work performed during the period 1 April 1991 through 31 August 1992 by the Georgia Tech Research Institute (GTRI) under NASA Marshall – a haunted house virginia woolf pdf Fiber optic (FO) strain sensors are a promising new tech-nology for advancing the state of the art in in-situ landslide monitoring. General performance advantages include high resolution, rapid sampling rate, multiplexing potential, and insensitivity to electrical disturbances (such as lightning). To date, however, there are only a few cases where FO strain sensors have been used for
An optical fiber having at least two cores positioned in a common cladding can be fabricated to be responsive to strain or hydrostatic pressure but not to temperature through the selection of materials, spacing and shape of the cores and cladding in the fiber.
fiber-optic interferometric strain sensor The interferometric sensor configuration is shown in fig. 2 and utilizes the frequency-modulated phase-generated carrier (FM-PGC) interrogation method.
A new class of intrinsic fiber-optic strain-displacement sensors based on the precisely controlled nonlinear buckling of optical fibers and the resulting optical bend loss is introduced. A multimode fiber version of the sensor is described that exhibits a sensing range convenient for many structural
In fact, fiber optic sensors are much more resistant to improper installation practices. A test article instrumented with strain gauges and fiber optic sensors. The gray wiring is for 21 strain gauges and the yellow is a fiber optic lead cable for a sensing fiber with approximately 625 sensing points. The sensing fiber, which typically has a diameter of 195 micron, has a negligible mass, which
ge R extr exas irginia Fiber Optic Strain Sensor for Planetary Gear Diagnostics NASA/TM 2011-217123 November 2011 AHS 2011 000154 National Aeronautics and
Fiber Optic Strain Sensors Opsens Industrial
Twin-core, polarimetric and in-fiber Bragg grating temperature and strain sensors for point and distributed measurements are reviewed. New applications to the in-situ monitoring of polymer composites are reported including techniques for measuring stress waves, resolving principal stresses and determining flexural strain variations.
An optical fiber sensor surface bonded onto a host structure and subjected to a temperature change is analytically studied in this work. The analysis is developed in order to assess the thermal behavior of an optical fiber sensor designed for measuring the strain in the host structure.
A Fiber Optic Sensor for Transverse Strain Measurement by C. M. Lawrence, D. V. Nelson, E. Udd and T. Bennett ABSTRACTmA fiber optic sensor capable of measuring two
OSP-A & OSP-FP fiber optic strain sensor probe and transducer

FIBER OPTIC DISTRIBUTED STRAIN AND TEMPERATURE SENSORS
Due to the difference in the physical and mechanical properties between the optical fiber, protective layer, adhesive layer, and the host material, the strains measured by a fiber Bragg grating (FBG) sensor may not be the actual strains of the host material, which impedes the reliable applications of FBG sensors.
ii Abstract In this project, we evaluated the measuring capabilities of a high-resolution fiber-optic strain sensor based on a miniaturized Fabry-Perot interferometer.
A novel fiber optic distributed sensor for temperature and strain measurements in building constructions has been developed and studied which is a composite optical element in the form of a reinforced single-mode optical fiber placed directly in the body of a fiberglass armature.
EFO Fiber Optic Strain Sensor Description The EFO is a fiber optic strain sensor especially designed to be embedded in concrete, ideal for composite material engineering research and civil-engineering applications such as monitoring stresses in structural mem-bers of buildings, bridges, tunnel linings and supports during and after construction.
A surface attached fiber‐optic sensor has been evaluated for maximum strain measurement capability in simple tension experiments to better understand the basic mechanisms of fiber‐optic sensor failure.
OSA Wide-range fiber-optic strain sensor

Rockslide deformation monitoring with fiber optic strain
Fiber optic distributed strain and temperature sensors measure strain and temperature over very long distances and are an excellent tool for monitoring the health of large structures. These sensors leverage the huge economies of scale in optical telecommunications to provide high-
The sensors could be connected to the monitoring unit via a single pair of fiber optic cables, thus greatly reducing cabling costs compared to if the company had to use traditional strain gauge sensors.
An interferometric-fiber-optic sensor and an efficient fringe-detection scheme are described. The fiberoptic interferometer consists of two fibers; they are labeled the reference fiber and the sensing fiber. The reference fiber is arranged in a circular pattern, whereas the sensing fiber is arranged in an ‘S’ pattern. These fibers are exposed to the same strain field and each experiences a
Model FP4000 Fiber Optic Strain Gage. Applications The Model FP4000 Fiber Optic Strain Gage is designed to measure strain in or on… Tunnel linings Bracing Struts Bridges Containment vessels Reinforcing bars Fiber Optic Strain Gage Model FP4000. The GEOKON ® logo and word mark are registered trademarks with the United States Patent and Trademark Office. GEOKON ® maintains an …
Optical strain sensor to be bolted or welded NT – Implementation of fiber optic sensors-E-0316.pdf Langues : EN Applications Notes. OFFSHORE MONITORING – Optical monitoring of force, strain, load … in marine conditions NA-17P-OFFSHORE MONITORING-E-0616.pdf
Fiber optic sensors are starting to be widely used for in-service monitoring of high responsibility structures by measuring strain or deformation fields. Several arrangements are
In most strain sensing applications, the protective coating over the fibers plays a crucial role in transfer of strain to the fiber core. The effect of the protective coating in each of these fibers is observed. Three fibers were used in our experiment.
Fiber Optics Strain Sensors optical losses at the fiber are irrelevant, but still 1550 nm, called C-band, is the preferred windows, because optoelectronic components are more easily available.
Using the fiber-as-a-sensor approach, operators benefit by installing specialized fiber optic cables along pipelines to gather strain events over great lengths in real-time. Taking advantage of Stimulated Brillouin backscatter (interaction of light with glass materials), DSS cables detect strain variation events associated with lengthy structures like pipelines and bridge spans. Furthermore
Product Specification. SFO-W Fiber Optic Spot-Welded Strain Sensor. The SFO-W is a fiber optic spot-welded strain sensor designed for civil engineering applications such as the monitoring of dams, bridges, tunnels, and other structures.
technology opportunity Lightweight Fiber Optic Sensors for
DTS0115 OZ Optics reserves the right to change any specifications without prior notice. 3 January 2018 1 Fiber Optic Distributed Strain and Temperature Sensors (DSTS)
Experiments and Results , To test the performance of the Bragg grating laser strain sensor a Bragg grating was adhered to the surface of a cantilever beam and the wavelength of the fiber laser measured as a function of the
Fiber optic strain sensors are welded directly to the surface of the metal structure (pipes, beams, etc.), and it has a protective silicone cover. Fiber optic strain sensors are durable and stable, widely used for civil engineering constructions, particularly they reinforce concrete structures exceptionally well.
A wide-range strain sensor which utilizes optical fiber as the transducing element is reported. This device differs from the well-known microbend type sensor in that a roller chain is used to impose constant curvature bends on the fiber, rather than a corrugated plate which imposes sinusoidal bends in the microbend sensors. This change also
Fiber optic sensing technologies collect strain and temperature data about a structure in order to validate structural and thermal models, ensure structural …

Thermal Strain Analysis of Optic Fiber Sensors
Fiber Optics Strain Sensors NATO
– Fiber Optic Strain Sensors althensensors.com
Fiber-optic strain-displacement sensor employing nonlinear
Fiber-optic Sensors RP Photonics
Real-Time Fiber Optic Strain and Shape Sensing (FOSS
FIBER OPTIC DISTRIBUTED STRAIN AND TEMPERATURE SENSORS
Structurally Integrated Fiber Optic Strain Sensing of
In most strain sensing applications, the protective coating over the fibers plays a crucial role in transfer of strain to the fiber core. The effect of the protective coating in each of these fibers is observed. Three fibers were used in our experiment.
Fiber optic sensing technologies collect strain and temperature data about a structure in order to validate structural and thermal models, ensure structural …
hydrophone sensors is a measurement of fiber strain via the strain induced phase change in a light field. A large-scale sensor array system requires many channels multiplexed onto a single fiber,
An optical fiber sensor surface bonded onto a host structure and subjected to a temperature change is analytically studied in this work. The analysis is developed in order to assess the thermal behavior of an optical fiber sensor designed for measuring the strain in the host structure.
The HBM FiberSensing range of optical (FBG) strain gauges and sensors is the perfect choice for demanding testing and monitoring applications. Previous Next High-Performance Optical Fiber Sensors
FIBER OPTIC DISTRIBUTED STRAIN AND TEMPERATURE SENSORS
A wide-range strain sensor which utilizes optical fiber as the transducing element is reported. This device differs from the well-known microbend type sensor in that a roller chain is used to impose constant curvature bends on the fiber, rather than a corrugated plate which imposes sinusoidal bends in the microbend sensors. This change also
EVALUATION OF A FIBER‐OPTIC SENSOR FOR STRAIN
Nonlinear fiber-optic strain sensor based on four-wave
Fiber Optics Strain Sensors NATO
Using the fiber-as-a-sensor approach, operators benefit by installing specialized fiber optic cables along pipelines to gather strain events over great lengths in real-time. Taking advantage of Stimulated Brillouin backscatter (interaction of light with glass materials), DSS cables detect strain variation events associated with lengthy structures like pipelines and bridge spans. Furthermore
Fiber-Optic Strain Sensor with a Millimeter Class High